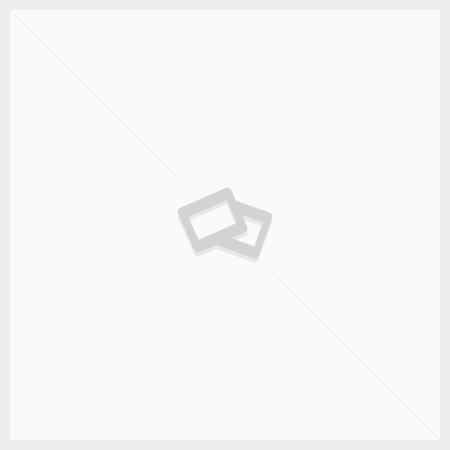
How Multi-Point Calibration Improved Compliance Reporting
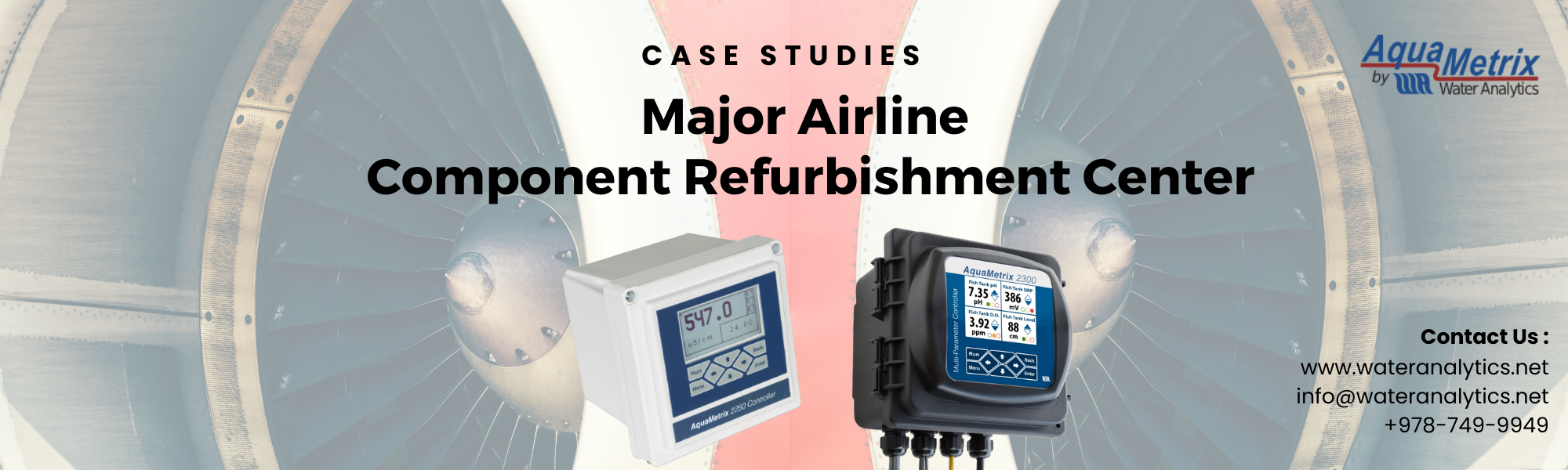
Case Study – Major Airline Parts Refurbishment Center
The Problem
Every year over 200 million travelers flying to 300 destinations in 50 countries with thousands of departures daily utilizing a major US airline’s service. With over 90,000 employees, thousands of aircraft in eight different size classifications and a global reach that is unparalleled, this airline is committed to providing their customers the safest travel experience possible.
Maintaining their planes at peak performance is a major cost and the airline refurbishes parts in its own Parts Refurbishing Center. The center maintains, repairs, and overhauls aircraft engines manufactured by GE, Pratt & Whitney, and Rolls-Royce. The plating shop consists of 146 tanks and the cleaning shop has more than 30.
Conductivity and pH measurements are key to maintaining water quality in rinse tanks. The tanks in the plating shop tanks contain high levels of sulfuric acid, hydrofluoric acid, nickel etch, nickel plate and various degreasers—all of which make up for a very hostile environment. The tanks in the cleaning shop must be maintained at conductivity levels less than 20 µS/cm.
The Parts Refurbishing Center had used instrumentation from one of the largest manufacturers but struggled to achieve consistent, accurate results, thus costing the facility valuable manpower, money, and time. Facility managers searched for alternatives. In particular, the constraint of calibrating conductivity at only one point meant that conductivity readings would only be accurate at levels within one order of magnitude at that point. The result was frequent “Out of Tolerance” reports that required immediate attention.
The Solution
Harrington Industrial Plastics, a key supplier of piping, fittings, and instrumentation to the airline, recommended AquaMetrix sensors and controllers. In the first two years the refurbishing center purchased AquaMetrix AM-2250 controllers and AS series conductivity sensors. The AM-2250 gave them the ability to calibrate at more than one point, as in most controllers. (As many as 16 points are possible.) The result was accuracy over a much wider conductivity range. In addition, the third-generation conductivity circuit provided extremely consistent measurements and the user interface was much easier to navigate.
More recently the refurbishment center started using the new ES-1 toroidal conductivity sensor with the AM-2251 controller. The circuit in this controller is unique in that it gives accurate readings from 4 to 400,000 µS/cm. This unparalleled wide range allows them to streamline to one sensor, allowing them to save both time and money. The toroidal sensor is unaffected by fouling, such as that caused by plating or suspended solids. According to the Facilities Manager, “We save a lot of time and money because we no longer prematurely flush the rinse water to our wastewater plant. We do not spend time endlessly calibrating the equipment. This is a big improvement over the previously used products. I have been very pleased with the performance of the AquaMetrix system’s They are reliable and easy to use, making our department more productive and efficient.
For more information about Aquametrix Controllers contact Brian Gannon at bgannon@wateranalytics.net